Ing. Gustavo Adolfo López Fajardo, TURBOALEACIONES S.A. DE C.V.
En las estaciones de compresión de gas y plantas de proceso, es común que las condiciones de diseño que determinaron la selección de los equipos de compresión cambien con el tiempo. Existen muchas variables que influyen en esos cambios, como lo son la modificación de temperaturas y presiones en los procesos, cambios en los requerimientos de flujo y cambios en la gravedad específica del gas a ser comprimido, entre otros.
Ante estos cambios, una alternativa es reemplazar los equipos por maquinaria nueva. Sin embargo, no siempre es la mejor solución, ya que en muchas oportunidades el costo del reemplazo es muy alto. Lo anterior debido a que no solo incluye el precio de los equipos nuevos, también se deben considerar las modificaciones mecánicas a las tuberías de proceso, modificaciones a cimentaciones, cambios en las acometidas eléctricas y de instrumentación.
Los cambios en la producción de gas natural, en los yacimientos del sur del país, obligan a que ahora se deba llevar gas del norte al sur. Para satisfacer esa nueva necesidad, debían hacerse modificaciones en una de las principales estaciones de compresión. El proyecto se licitó y nuestra propuesta resultó ser la más conveniente a los intereses del cliente.
Continúa leyendo: ¿Cómo reducir gastos en turbomaquinaria?
El primer reto fue afrontado por nuestro equipo de diseño. Se requería modificar la aerodinámica del compresor centrífugo de tal manera que permitiera cumplir con los nuevos requerimientos: gas natural con propiedades diferentes a las del diseño original, cambio en las presiones de succión y descarga, cambio en la temperatura de succión y mayor rango de flujo de gas a comprimir. Todo esto, utilizando el mismo equipo motriz, turbinas a gas aeroderivadas, por lo que el rango de potencia disponible y de velocidades no podía cambiar. Después de intensas jornadas de configuración y optimización del diseño aerodinámico, se generó el mapa del compresor centrífugo que permitió satisfacer todos los requerimientos (Figura 1).
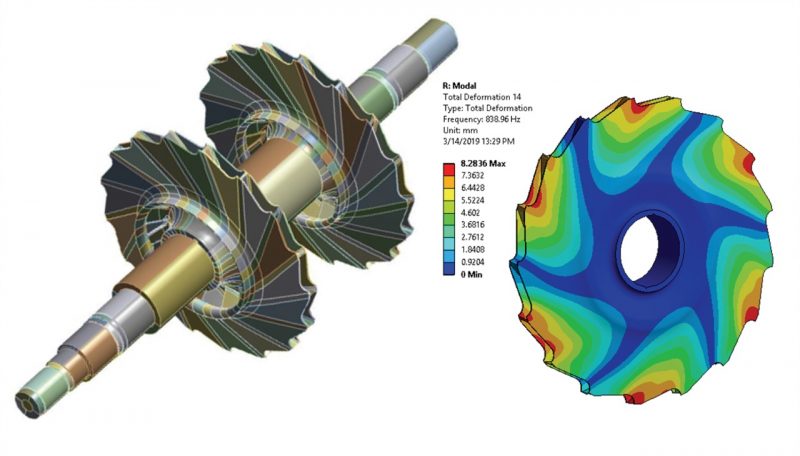
Figura 2. En la ingeniería se realizaron estudios especiales, entre ellos análisis por elementos finitos para determinar esfuerzos y deformaciones en los componentes. Las imágenes corresponden a parte de los estudios en los impulsores.
De allí, la responsabilidad pasó a manos del equipo de manufactura de nuestro Centro de Servicio. Quienes, con su gran talento, convirtieron planos y aceros especiales en “piezas de arte” que giran a alta velocidad.
Figura 3. Detalle del perfil aerodinámico y vistas del impulsor antes de prueba de sobrevelocidad.
Finalmente, ejecutamos la instalación y puesta en servicio de los compresores. En esta etapa se confirmó que nuestro rediseño cumplió con las exigencias contractuales.
Figura 4. Proceso de instalación de los internos del compresor. Se diseñaron y fabricaron herramientas especiales para garantizar un armado adecuado del compresor.
Este valioso trabajo ejecutado por dos empresas orgullosamente Mexicanas con una estrecha relación comercial, Turboaleaciones SA de CV y Turbomáquinas SA de CV, fue desarrollado exitosamente sin accidentes ni atrasos en el tiempo de entrega.